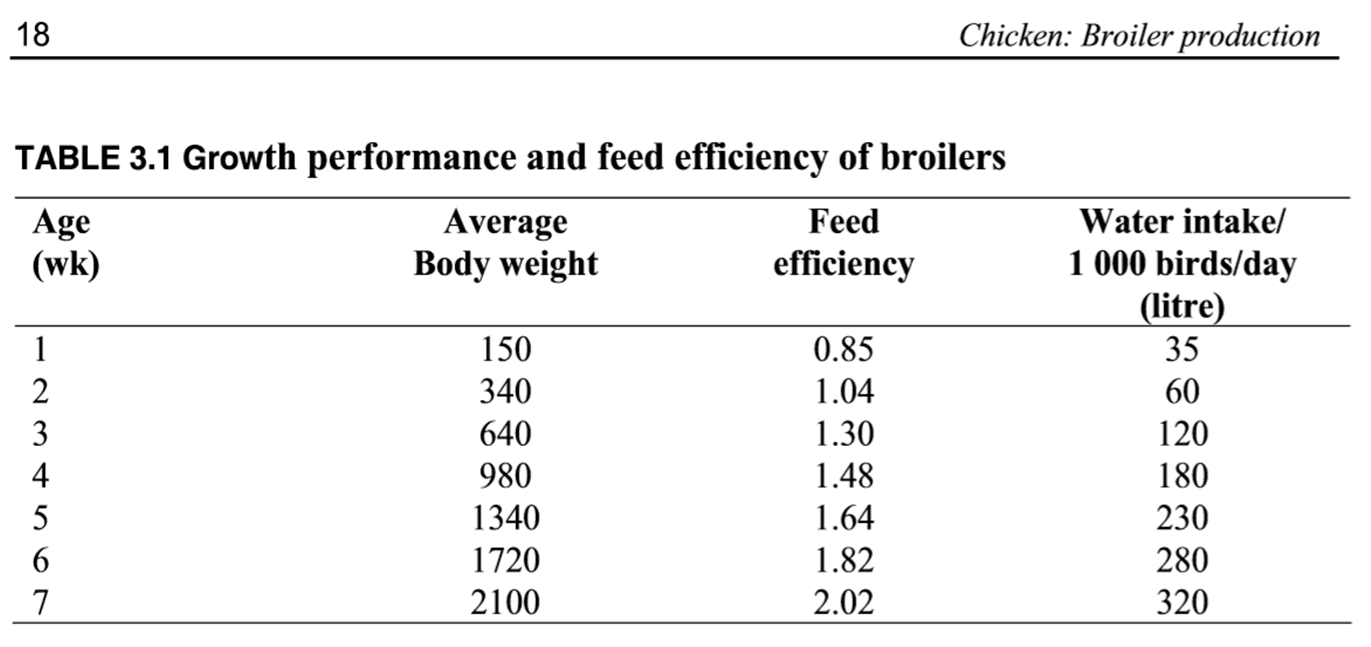
There’s a now pro way of looking at your cost of rearing layers or broilers that could SERIOUSLY help you smash those ROI targets.
I call it:
(“Econo-Poultry Technique.”)
I recently refined this strategy and packaged it in the new version of our in-house poultry consultancy software: Poultry Project Reporter 2.0
And in today’s discussion on the economics of raising chicken either for meat or eggs, I’ll share with you exactly how I did it (and step-by-step).
[Can’t read it all now? Download the PDF, by clicking on the orange button above.]
Opportunity Cost
Opportunity cost is, without doubt, the BIGGEST hidden cost in starting a poultry farming business.
When calculating the potential return on your poultry farm investment,
You’ve probably not accounted for opportunity cost.
(If you haven’t, you’re not alone.
In fact, when I posted this premium newsletter on ‘opportunity cost’ to my email subscribers recently, I received a HUGE response. )
99.9% of small & medium-sized business owners totally ignore this iceberg of ship sinker.
Before my brief experience of working for a business broker, I didn’t really have opportunity cost on my radar either.
But things changed when I got schooled on this critical ROI planning technicality.
What is opportunity cost?
If you’re new to the phrase,
Opportunity cost is the very real and tangible (yet indirect) cost of having your money, time and resources tied up in an investment…
…when you could have ploughed that potential elsewhere.
It’s not to breed doublemindedness and indecision.
Far from it.
It’s actually a way of shoring up your confidence in the decision.
Here’s how…
In assessing the opportunity cost of starting your poultry farm you perform what professional project managers call:
Alternatives analysis.
In this short paper exercise, you literally compare in a head-to-head fashion the future prospects of alternative investments you might choose instead…
…against the projected financial benefits of running your broiler or layer poultry farm.
A short story
Beginning…
Let’s say,
That you calculate that your 1,000 layer flock would bring you in $11,000 EBITDA (net profit) per annum in egg sales alone.
Over 6 years (with a 1st-year climb to reach peak performance) you could expect your layer poultry farm to net you $54,000.
But the business, according to your figures, might cost you $20,000 start-up investment.
The net benefit over 6 years would then be $34,000 for running the poultry project.
Middle…
Now, at the same time as planning your poultry farming business,
You get an offer from a friend to buy an online business.
It will cost you $12,000 and on the books, it currently generates $333.00 per month (it is being sold to you for a multiplier of 36 times the monthly revenue.)
The web business has a lean cost model and $300 of the total revenue figure is net (take-home) profit.
Over 6 years, this venture would NET you ($300*72 months):
$21,600.
The other fact to account for is your time involvement.
The web business runs on 2 hours per week commitment.
Your poultry business would require perhaps 25hrs+.
The cost in wages or time expense over 6 years would be around $50,000.
Calculating opportunity cost
The opportunity cost of you starting the poultry farm would be ($21,600 + $50,000) – $34,000 = – $37,600
In other words, by this crude estimation, you would be $37,60o worse off for choosing the layer business.
Not so fast!
But like I said this is a rather crude view,
What about:
- your plans to rapidly scale the layer operation
- manure sales
- spent hen sales
- money saved on household expense on eggs and culled hen chicken meat
- hiring out your egg packing equipment to other local farms
If from these points alone, you estimate an additional benefit of, say $45,000 over the next 6 years.
Your opportunity cost works out to be:
($21,600 + $50,000) – ($34,000 + $45,000) = +$7,400
i.e. You’ll be $7,400 better off in poultry.
(Not to mention – the lifestyle benefits of being in agribusiness.)
Poultry Economics
The poultry farming business is constrained or defined by some pretty fixed parameters.
These factors have their own relationship to the costs involved in raising the birds.
Here are some examples:
Broiler vs. Layer Production Cycle
Broiler meat chicken typically in commercial rearing take somewhere between 6-7 weeks to reach marketable weight.
The equivalent optimal time frame for rearing layer chicken is about 72 weeks in commercial farms.
The point at which the cycle hits the endpoint is called Break Even.
In other words,
If you keep commercial layer birds any longer than the point of break-even (~72 weeks generally speaking) then you begin losing money to keep them.
(i.e. the cost of rearing them exceeds the revenue gained from egg sales.)
The same applies to commercial broiler chicken.
Keeping them beyond 6-7 weeks becomes loss-making. The direct cost to keep them starts to overshadow the sales revenue from selling the birds.
The Hatching Eggs, Day Old Chick & Pullet Race
These three options for starting poultry production are like choosing lanes before a 200m race.
Each has its own cost advantages and disadvantages.
(They all amount to the same distance – but your preference is simply based on how you see things.)
Here’s how they line up:
Hatching your own
With both broiler and layer farming, you can choose to hatch your own chicks to raise.
This is starting on the inside lane.
You seem further away from the end than the other lanes at the start, but it’s an optical illusion.
Yes, you run the costs of buying the fertilized eggs and incubating them until the successful ones hatch.
But you save on the cost of paying for a day old chick or even a pullet (if you run a layer farm).
Sellers of birds make back their rearing costs
As you can imagine sellers of day-old chicks and pullets charge much more for these than fertilised eggs.
They recoup their costs of rearing the birds by charging a price that covers their expenses,
PLUS gives them a healthy margin of profit.
So, going back to the sprint race analogy,
Buying day-old chicks for your broiler or layer farm is like taking up the middle lane.
And if you produce eggs, buying pullets is the outside lane.
The long and short of where you start off
Basically, each course runs the same length.
But because of the offset difference from the lane orientation,
The runners start at different positions on the track which at the beginning might seem like some are at advantage whilst others are at disadvantage.
But it all adds up to the same at the end.
“And the medal goes to…”
The key is not caring where you start, but mentally blocking out all distractions and running YOUR best race.
Bird Development Stages
When calculating the costs of raising chicken,
You’ve should also account for the constant flux of input volume (amount) and velocity (speed) throughout their growth stages.
Plus, the differing nutritional demand of birds at different ages.
The combination of factors leads to fluctuating cost burden.
But this is a slightly simplistic view of things.
Because with a muli-flock model – these changes are smoothed out by the layering of needs.
One flock’s needs insulating against the farm’s exposure the needs of another…in a staggered fashion.
This brings us on to…
Inputs (Direct costs)
These are your classic direct costs or the cost of goods sold (COGS).
Investopedia classifies these as being:
“Cost of goods sold (COGS) refers to the direct costs of producing the goods sold by a company.
This amount includes the cost of the materials and labour directly used to create the good.”
In the sense of your poultry farm,
These are relatively easy to figure out…
To produce a table bird or a table egg, your need:
- a bird (either from a fertilized egg, day-old chick or pullet)
- feed & nutritional supplements/additives
- water
(Depending on your model of production, you could also include within this cost of vet care/meds etc.)
Now, let’s examine these costs…
Bird (Egg i.e. hatch your own, DoC, PoL)
As I said earlier,
The cost of acquiring each bird is like choosing your lane to run in – if you think of poultry farming like a race.
Let’s look at some real example costs,
And how this choice of start point will affect your farm’s cost model.
These are some example prices from hatcheries in the United States:
- Hatching egg cost = $2.50
- Day-old chick = $7.50
- Point of lay (PoL) hen = $22.00
As percentages of the point of lay cost, here’s how they line up:
- Day-old chick = 34% cost of PoL
- Hatching egg = 11% cost of PoL
And if we line up hatching egg cost vs. day old chick cost, we get:
- Hatching egg = 33% cost of day-old chick
Whilst these numbers by themselves don’t tell us much,
If we look at them in the light of production and yield we learn a little more.
Egg-laying
Peak egg production (according to the HyLine Commercial Brown management guide) occurs at about week 22-23.
At this point, commercial strain layer bird, like the HyLine Commercial Brown should achieve a hen-day egg production of ~90%.
This is the part every layer farmer looks toward,
Because the birds begin earning back.
Before then, your farm bears the brunt of having to fund the rearing without return.
The longer the delay to peak laying…
…the longer your farm’s delay to earning back (recouping) the cost of pre-lay rearing.
Broiler meat birds
Conventional broiler birds are reared for 6-7 weeks and then marketed.
There isn’t a pullet equivalent for broiler farming.
At maturity, the bird itself is harvested, and so all gains must have been made beforehand.
This leaves only hatching eggs or day-old chick as viable start points for broiler farming.
Again, hatching eggs costing about a third of the price of a day-old chick, typically.
(Sellers of birds, rather than eggs, passing on the cost of rearing to their customers.)
Feed Consumption
Broilers
According to the Broiler Management Guide written by Livestock Feed Ltd.,
The average conventional broiler breed bird will consume approximately 5.3kg in 6-7 weeks of rearing.
Estimating the cost of feed across the entire rearing period isn’t directly linear (straight forward).
At each stage of growth:
- brooder
- grower
- finisher
…optimal growth yield is achieved by feeding birds with their appropriately formulated age-related feed ration.
Each type of feed is priced slightly differently on the basis of a different balance of ingredients.
But taking an average, in Nigeria broiler feed could fetch for ₦240.00 per kg.
So the equivalent cost of feeding a broiler bird from day one to week 6-7 is roughly speaking:
₦1272.00
Layers
Again the HyLine performance sell sheet indicates that their layer strain, Commercial Brown hens, consume:
~49kg of feed in 72 weeks.
The equivalent feed cost to rear layers will be ₦17,280.00
By comparison, the cost of feeding layer hens through a full production cycle is:
…13.5 times more than rearing a broiler bird (through its equivalent production cycle of 6-7 weeks).
In context
But we can never just look at cost in isolation.
The cost has always got to be viewed in the light of ROI to assist in strategic decision making.
Just think,
An average layer is likely to lay some 330 eggs in the space of 72 weeks, from a one-day-old starting point.
At an average price of 12c ($0.12) per egg,
Each layer hen is scheduled to generate some $39.60 over the course of its commercial lifetime.
By comparison, broiler chicken might be sold for $4.7 ($1.62 x 2.9kg per bird).
Now, put this in the context of your previously cost of feeding broiler or layer birds and you can quickly arrive at a profitable conclusion.
Other Direct Costs
Aside from the principal direct costs (as I call them), being:
- cost of bird
- feed cost
There are other costs associated with production in broiler and layer farms.
Namely:
- labour
- vet fees
To factor these in, we apply two different calculations.
Labour is calculated at:
- an hourly wage (multiplied by)
- by the number of staff members (multiplied by)
- the number of hours worked within the time period
The product of this equation is a simple wage bill.
For vet and med fees, I apply a flat fee per bird. The total bill absorbed equally by each member of the flock.
This method is called absorption costing.
(A neat way of accountants spreading overhead costs across products and services sold.)
When you use this method you end up with a useful yardstick for estimating vet/meds cost per bird.
You simply calculate a flat fee, which can then be multiplied by the heads of the flock.
But what about one-off costs?
One-Off Capital
Starting a poultry farm typically involves some one-off costs too.
These are usually asset purchases.
Items like:
- land
- building construction
- equipment
- vehicles
…are bought once and will be used repeatedly until the end of their useful life.
This brings us on to…
Depreciation
Most physical assets need replacing or deep restoration after some time.
This cost is a very real deduction from your business budget.
And in most cases unavoidable and entirely expected.
Plan ahead.
In common business accounting practice,
The funds separated for replacing a physical asset when it becomes spent is called depreciation.
Proactively, your poultry farming business should include depreciation within your income statement as an expense.
You’ll want to plan for this expense, otherwise, if you overlook it, you’ll be caught off-guard when you least expect it.
Without ringfencing money for this,
Say, if your layer farm had to replace your delivery van after 6 years of continual use,
Coming up with say, R200,000 (South African Rand) on the spot could be difficult.
(Depreciation to the rescue.)
Working Capital
When starting a poultry farm,
You’re going to need to ‘prime the pump’ before you generate sustainable cash flow.
So, in the first instance – at least for the first year of trade – you need to fund your own operating expenses.
Buying:
- birds
- feed
- rent/mortgage
- transport costs
etc. will have to be financed with cash either from your own supply or from external investment.
This is known collectively as working capital.
In other words,
The money you need to run the operations until it becomes sustainable.
For example,
If you calculated that running a 30,000 layer egg production farm in the Philippines would cost you ₱14,063,140.00 in bird feed for the 1st year,
+ ₱600,000.00 in chick costs for your 1st 30,000 birds in 3 separate batches.
The working capital for year 1 would therefore be these two figures (₱14,063,140.00 + ₱600,000.00),
PLUS other direct costs – like labour etc.
Then lastly, you’d add the overheads (indirect costs) on top…
Overheads (Indirect costs)
These are a bit like what they sound like.
Costs that will hang over your head whether you produce or not.
Costs like land rent, for example.
They are not directly related to production,
But, granted, without rent paid and the farm occupation legitimate you simply cannot run a successful poultry farm.
So overheads can be really important costs.
With calculating overheads, there could be different approaches for handling each item,
But the bottom line is a grand total of indirect costs of the poultry farm.
Now, onto funding…
Borrowings
Poultry farming ventures are usually either self-funded or financed on borrowings.
Actually, poultry is one of the few livestock-related agri ventures that can be started VERY small and scale quickly.
Zero-debt is great because it’s lean.
(Less expense.)
Loan repayments are an unavoidable business expense, where you have debt.
(And so, debt horrendously undercuts your profits.)
For example,
I recently came across a PDF project report of a 20,000 layer farm published by the West Bengal Poultry Federation.
In the loan statement, they published a loan requirement of 127 Lacs.
This got me thinking…
…How much would the repayment on a loan like that be?
I fired up Poultry Project Reporter software – and only a few minutes later…
A loan of 127 Lacs to finance a 20,000 layer farm start-up at 6% interest would mean Rs.210,475.68 monthly repayment over 72 months (6 years).
This being taken directly out of your bottom line, whether things are going to plan or not is a steep start.
(Ouch.)
Middleman/Intermediary inc. FX or commission
Just like finance, a common thought is that you need middlemen to make a market tick.
Whilst they do work to aggregate transactional opportunity,
In other words – put people together who might trade (buy and sell),
Their involvement is not essential.
Much like any part of the industry which performs a service, but is non-essential:
Middlemen = COST.
Sales commission is the reward of their labour.
A slice of the action.
This percentage deduction is a business cost and should be accounted for in the overall cost of getting the product to the consumer.
Also, if you import the chicks, for example, a very real cost is foreign currency exchange (or FX).
In most cases, your bank will deal with the exchange.
But having worked in a corporate FX brokerage some years ago, I can confidently tell you that bank FX charges include some serious amounts of spread (profit).
To the tune of several per cent in most cases.
Brokerages can shave cost in this area, but you always need to walk into transactions with your eyes wide open.
Losing 5%, for example, on every trade to buy birds, feed etc. takes a significant amount of your take-home pay straight out of your pocket.
Inflation
Another secret cost threatening your poultry farming profits is inflation.
(The continually increasing cost of living – worldwide.)
This is one of the BIG costs to discount your poultry farm ROI projections by.
If you don’t tune down your expected earnings by the effects of inflation,
Then you end up with an INFLATED expectation on your future broiler or layer earnings.
This only leads to disappointment.
So always, always remember to discount poultry cash flow projections for:
a) opportunity cost, and;
b) the cost of inflation
In fact,
That’s EXACTLY why I built in a discounted cash flow feature into the Poultry Project Reporter software, that automatically adjusts your future expected cash flows by a set percentage.
For example,
To add the cost of inflation if you were planning a egg production farm in Uganda (based on 2020 figures),
You’d simply type into the PDF fillable web form ‘4.2’ (to represent the official Ugandan national inflation figure for 2020, which was up 45.57 % from 2019)
…the software will do ALL the rest and give you a PDF report of your Uganda poultry farm cash flow for 6 years,
Adjusted to inflation, of course.
No need for messy manual calculations.
All done for you.
Quick Percentages
Now,
That’s enough of the theory.
In this section,
I want to throw you some quick cost percentages that you might use to guide your own poultry farm cost calculations.
Here are the percentages (based on environmentally-controlled shed rearing conditions):
(Analysis based on sample data published by The National Bank of Pakistan)
Roughly speaking, a project of this size and nature would have SIMILAR benchmark costs.
But I must say it again, this is ROUGHLY speaking.
There’s no way that you could rely on these exact numbers for your cost plan.
If you think about it, there are just too many variables involved:
- where they sourced their prices from
- the state of the economy at the time or research
- availability of exact match items
- unique features of his project
- strategic preferences of the management team
…this list goes on.
So, the purpose of these percentages is to give you a ‘real-life’ feel of what a poultry project cost line up looks like.
Cost of comparative broiler systems in the Netherlands
I recently found this study on the “Economics of broiler production systems in the Netherlands” by Wageningen University & Research.
It’s a great insight into how your choice of broiler farming system directly influences your costs.
The four broiler systems compared within the study are:
- Conventional: fast-growing broiler and maximum density 42 kg/m2 poultry house.
- Dutch Retail Broiler (DRB): slower-growing broiler and maximum 38 kg/m2 and enrichment with straw
bales. - Better Life one Star (BLS): slower-growing broiler (slaughter age minimum 56 days), maximum 25 kg/m2
and a covered outdoor area. - Organic: slower-growing broiler (slaughter age minimum 70 days), maximum 21 kg/m2 and access
to an outdoor area.
Whilst you are probably familiar with the potential consumer health benefits associated with organic & free-range poultry farming over congenial rearing,
You may not have much insight into how the operational costs differ.
And WHY they differ?
Here’s a breakdown:
Characteristics of the broiler systems
The criteria above will help you better understand how each of the poultry systems works.
Technological factors and parameters
Here you see the operational differences between the 4 broiler systems.
The further you move away from conventional broiler farming towards organic, we see:
- longer growing periods
- lower mortality
- higher feed conversion
- more space is given to flocks of lower headcount
- longer empty periods
- fewer production cycles
Generally, decreasing operational efficiency for the sake of passing on product quality benefits.
Variable costs comparison of broiler systems
As a broad brushstroke statement,
We could summarise by saying – better product quality means higher direct costs.
Production cost comparison of broiler systems
Better broiler product quality and consumer nutritional benefits (with free-range and organic methods) come at the cost of the producer.
They generally have:
- Increased labour
- More fixed cost (overheads)
- Higher ‘non-feed, non-chick’ related variable cost of goods sold
- More expensive chicks
- Higher feed costs
Here’s why…
Increased labour
“…higher labour input due to a higher surface area per bird and extra labour for providing grain and straw bales.”
Organic and free-range (DRB, BLS & Organic) workers have to cover more area and have much more hands-on rearing duty than with environmentally controlled conventional farming methods.
More fixed cost (overheads)
“…the density is lower the costs per m2 poultry house have to be divided by a lower number of produced broilers per year. ”
“For free-range systems the fixed costs include the costs of land and fencing. The fixed costs increase as the growing period of the broilers is longer.”
Higher welfare, better product quality systems (DRB, BLS & Organic) cost more in general overheads, labour and capital asset expense than conventional systems.
More expensive chicks
“Day-old chicks of slow-growing breeds are more expensive than conventional breeds”
“For organic, the costs are extra high because of an extra vaccination in the hatchery.”
A price premium attached to slow-grow day-old chicks and additional vaccinations at the hatchery adds yet more cost to the higher welfare models (DRB, BLS & Organic).
Higher feed cost
We see a gradual feed cost increase from conventional to free-range (DRB & BLS) as the rearing cycle increases from 41 days to 56 days.
The longer rearing cycle carrying a higher feed consumption.
The largest increase, however, is seen when we switch to organic practices where we witness an almost 300% leap in feed cost.
This is due to a combination of higher feed costs for organic ingredients and also a rearing cycle of 75 growing days.
BONUS TIPs
And now, a couple of pointers to help you produce some really ROBUST cost projections for your poultry farming project.
RFQs
Gathering together supplier proposals and price quotes can be quite a chore.
It’s repetitive, detailed and time-consuming.
This is where a useful template (or proforma) would be worth its weight in gold.
Especially, one that was easily downloaded in PDF format.
Well, I’ve got one better than that for you…
How about a purpose-made PDF fillable web form that:
- calculates…
- formats…
- designs…
- publishes…
- auto-downloads as PDF…
…professional standard RFQ/RFP (request for quote/proposal) documents?
Click here to use it now (premium subscribers only).
Sensitivity Analysis
When putting together feasibility studies or project reports, you’ll want to put your mind at rest with some what-if scenarios.
The kind that help you report on outcomes when critical conditions change.
(…especially changes in costs, like feed or chicks.)
For such planning exercises, I recommend using sensitivity analysis:
Simply, you run side-by-side profit and ROI calculations, but with each attempt, you change a cost value.
For example,
I can use Poultry Project Reporter software to test my farm’s profit sensitivity to…
…say, a feed price increase of 25%, from ₱.26.00 to ₱32.50…
All I have to do is type in my new feed cost,
And now I see the gross profit contribution (over 72 weeks of rearing) of each egg-laying hen change from:
₱591.86
…to…
₱273.75
My next step will be to see how my operational profit lines up once all overheads are absorbed into that figure.
Will I still be in profit?
Perhaps that’s for another article.
Now, over to you…
Are you currently calculating the cost of rearing poultry?
Have you experience of rearing broilers or layers?
Do you think I missed something?
Either way, I’d be interested to hear from you.
Leave a comment below.
My name is Gladys.
I am looking to set-up a poultry farm in Botswana,Matobo village selling eggs.
My initial goal is to begin rearing 166 layer hens buying them at a point of layering on a small piece of land which I own. my land is a 20 hacters and has got a borehole with solar pannels i also own a toyota dyna truck,since i am working i will have an employee who will be staying on the farm.
I’m an accountant by profession, so I will need to build poultry house.…my intention would be to raise the hens in an open house (no cages)…
I just need a little direction, particularly with an approach to costing…
…So my start-up investment figure and ongoing operational expenses are accurate.
Please can you assist me?
Regards
Gladys.
Dear Gladys,
Thank you for your enquiry.
It’s good to hear of your plans to become fruitful by layer farming.
It seems like you already have the most critical capital requirements met with:
– (sufficient) land ownership
– fresh on-site water
– electricity supply via solar
– consistent farm labour
– transport for product delivery
– alternative source of investment, during early start-up phases
It’s also interesting to see your preference for an open (deep litter) poultry house vs. cages.
You’ve identified you need to build a poultry house.
My immediate advice would be consider capacity for growth. If you build a structure based on your immediate plans of 166 layer hens and begin growing your flock you’ll quickly find yourself becoming constrained and redeveloping at additional cost – not to mention disruption to continuity.
As for the aspect, siting and type of poultry housing – this would depend on a number of factors, including:
– budget
– on-site environmental factors
– age of adoption (day old or point of laying)
– model of layer farming
…amongst many others.
As for your costing model and profitability…
When our team writes project report for poultry farming start-up, we see the most influential factor on BCR (benefit cost ratio) is initial capital outlay.
The main issue being cost of land acquisition, housing and labour.
Followed, closely thereafter by operational cost effectiveness (operational profit) – which is largely (…upto 70% in exposure…) determined by feed cost.
In my opinion, you would do well to put together a professionally written project plan which would suffice as a strategic/financial roadmap for defining your optimal route to arriving at the economic destination you seek for your farm.
Such a plan would detail all of the milestones, obstacles, twists and turns which you could expect to meet along the way and give you sight of how you might navigate them safely in order to achieve success.
Typically you would write such a project report to span an operational duration of 6 years.
A document like this would test for feasibility and profitability.
Besides this, I advise you also equip yourself with a clear business plan which would suffice a framework or manual to tether your daily management of the farm business into a sure orientation.
Should you require our assistance with drafting such reports/plans for your layer farming business…
Feel free to get in touch, or simply order your strategic business documents here.
Thanks again for your contact.
Yours sincerely,
Temi @ The Big Book Project
Goodday,
I want to set a chicken farm for meat production in Ghana.
I am looking at starting with 1000 chicks.
I need assistance with the type of poultry housing that would be efficient and and cost effective.
Thanks for your consideration.
Good day
Please send me the PDF Case Study: Cost of Rearing Poultry pdf.
regards
Hello Rohin,
It’s done.
I’ve just sent you access to download the PDF.
Let me know how you get on.
Speak soon.
Temi
I came across your site today while foraging through the net to acquire more insight into egg production.
Am preparing to start start a farm with 300 point of lay, and will appreciate to get the cost analysis for feeding per month.
Thank you
Good day
Looking to start a poultry farm Boilers in particular. I have a land already need to build the pen and stock can you help me with budget and cost of 200 Boilers for 6 to 7 weeks thank you
regards
Gatis
from Nigeria